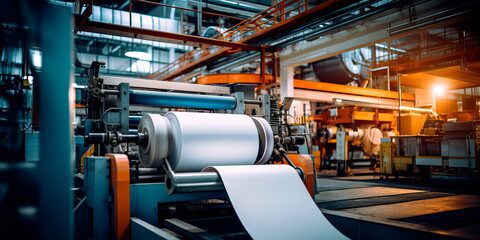
Filtration upgrade to reduce downtime
A customer in the pulp and paper industry had challenges with reliability and obtaining their desired filtration levels. They also had increased costs of operation du to the obsoleteness of their installations.
Customer’s concerns or issues
Technologies have evolved since the 70’s
Our customer was facing constant delivery delays due to the difficulty of finding replacement elements due to the obsolescence of the technology. The efficiency and their capacity to meet the cleanliness requirements was also a challenge. The elements used had a short life and translated into higher maintenance costs.
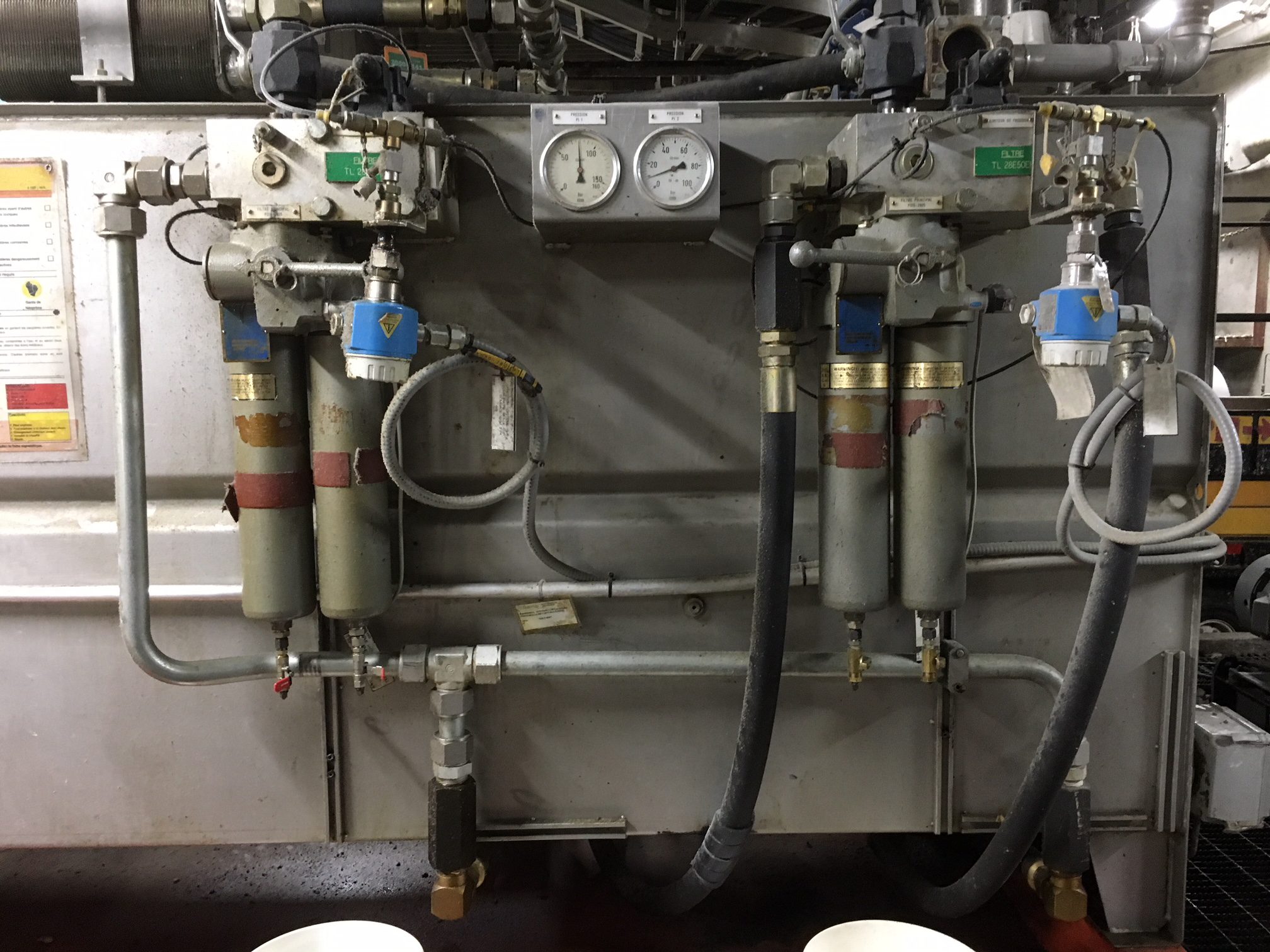
Installation before
Benefits of our solution
Higher cleanliness rating and reduction of component failures.
Our solution provided an extended life of elements thus reducing the maintenance needs and avoiding the unavailability of the replacement elements due to obsolecence.
50%
100%
80%
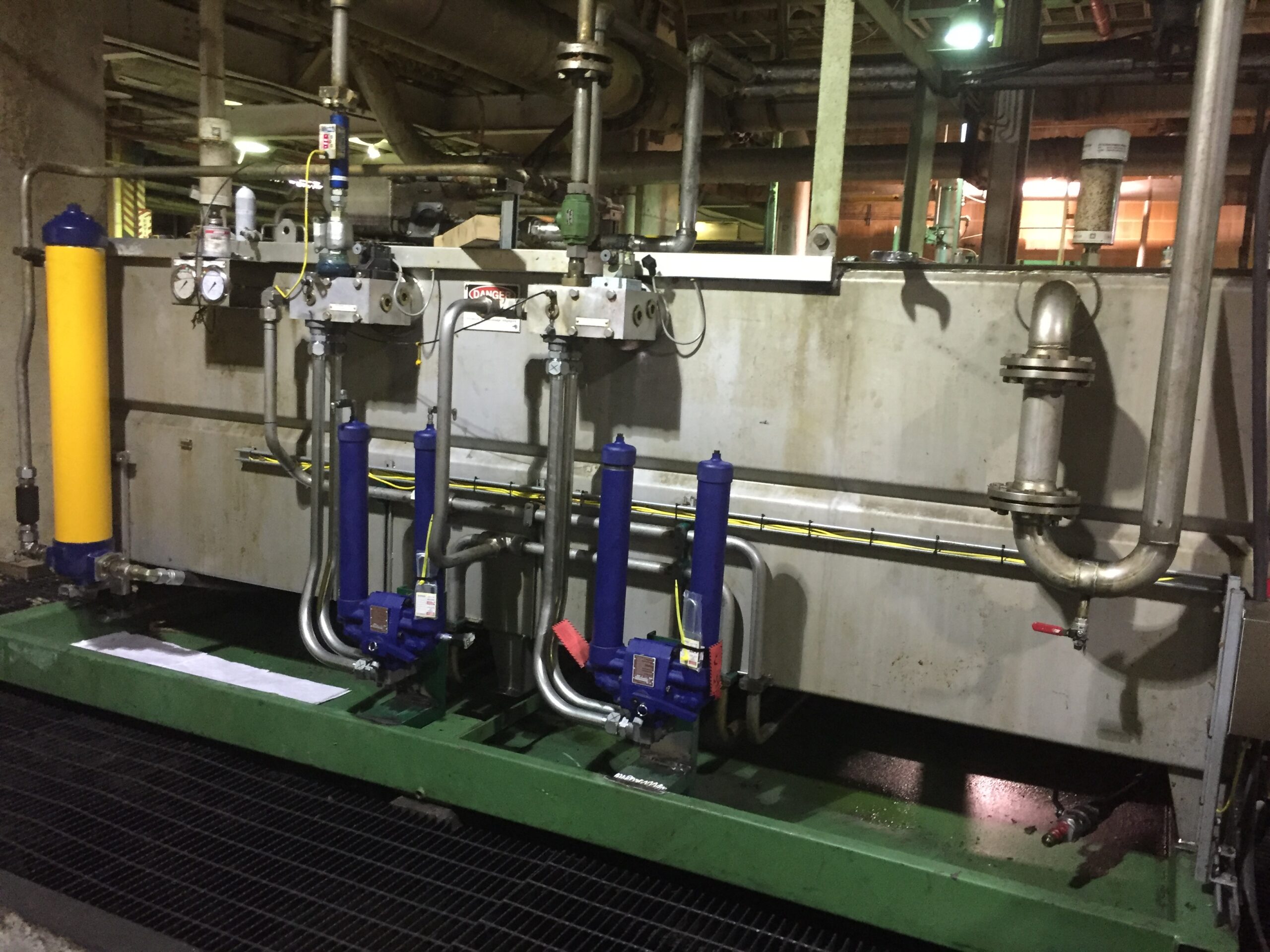
Installation with newest technology
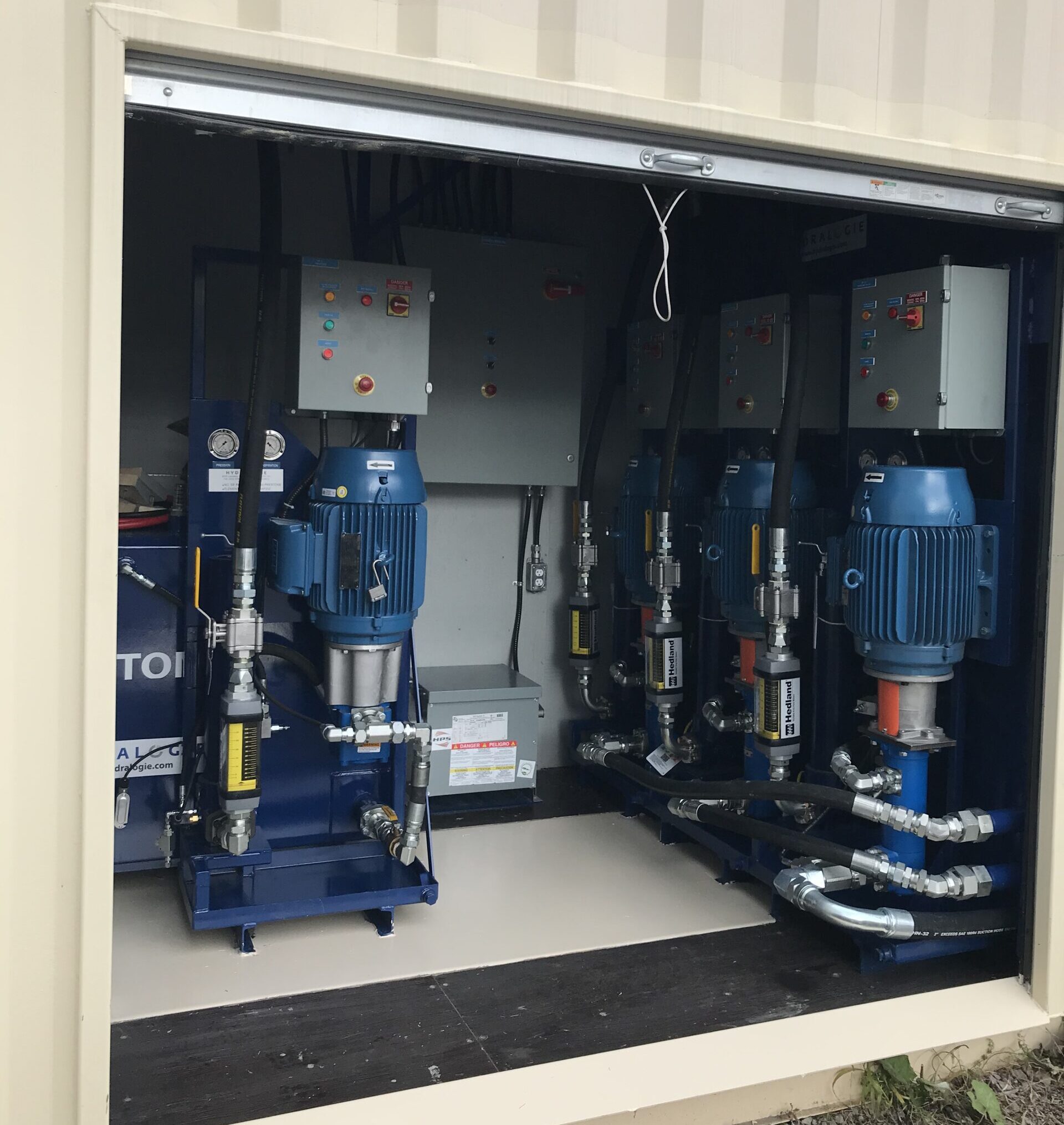
Next Case Study
Heated container for oil storage and distribution on mobile fleet
The customer did not have a distribution system for their mobile equipment outdoors. They had to transfer the oil from totes and barrels. The containers were kept outside affected by the weather and filtering the oil prior to or during the transfer was not an option and the oil viscosity was affected and slowed the transfer process.