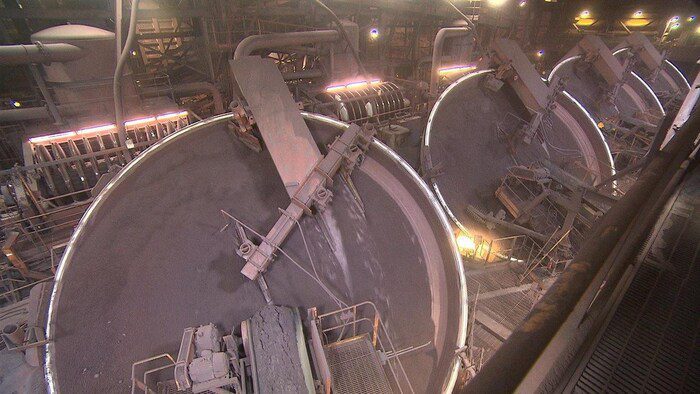
Mise en oeuvre d'un programme d'analyse de l'huile générant des économies substantielles
L’usine dépensait des sommes substantielles en déchets d’huile et en changements de réducteurs, l’huile étant remplacée de manière préventive, ce qui était coûteux et soulevait également des préoccupations environnementales.
Les préoccupations ou problèmes du client
Les mesures réactives en cas de défaillance étaient coûteuses
Le client devait changer de réducteurs en moyenne toutes les deux semaines et procédait à un changement d’huile en même temps. Ce processus était coûteux, chronophage et avait un impact environnemental négatif.
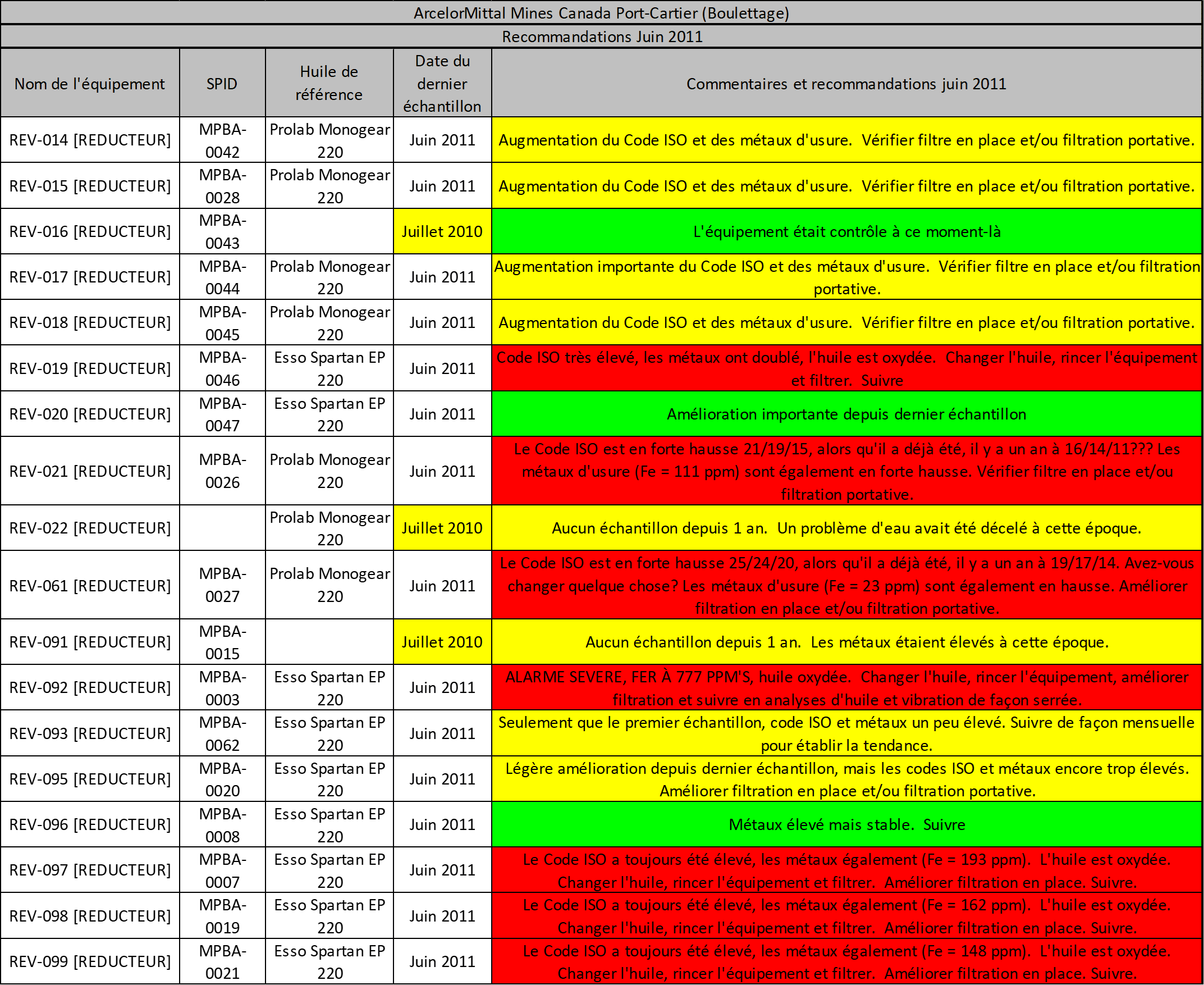
First sampling status report
Avantages de notre solution
Maintenance proactive et suivi de la santé des équipements
Notre solution consistait à mettre en place une vérification régulière de la santé des équipements grâce à l’analyse des huiles et à un plan d’action complet, éliminant ainsi la nécessité de fermetures imprévues. Des modifications de filtration ont été apportées aux composants clés pour résoudre les résultats anormaux et réduire le gaspillage d’huile avant la fin de sa durée de vie. En adoptant une approche de maintenance proactive, nous avons permis d’économiser des millions de dollars en dépenses de maintenance réactive et en arrêts non planifiés.
90%
650 000$
4 million de $
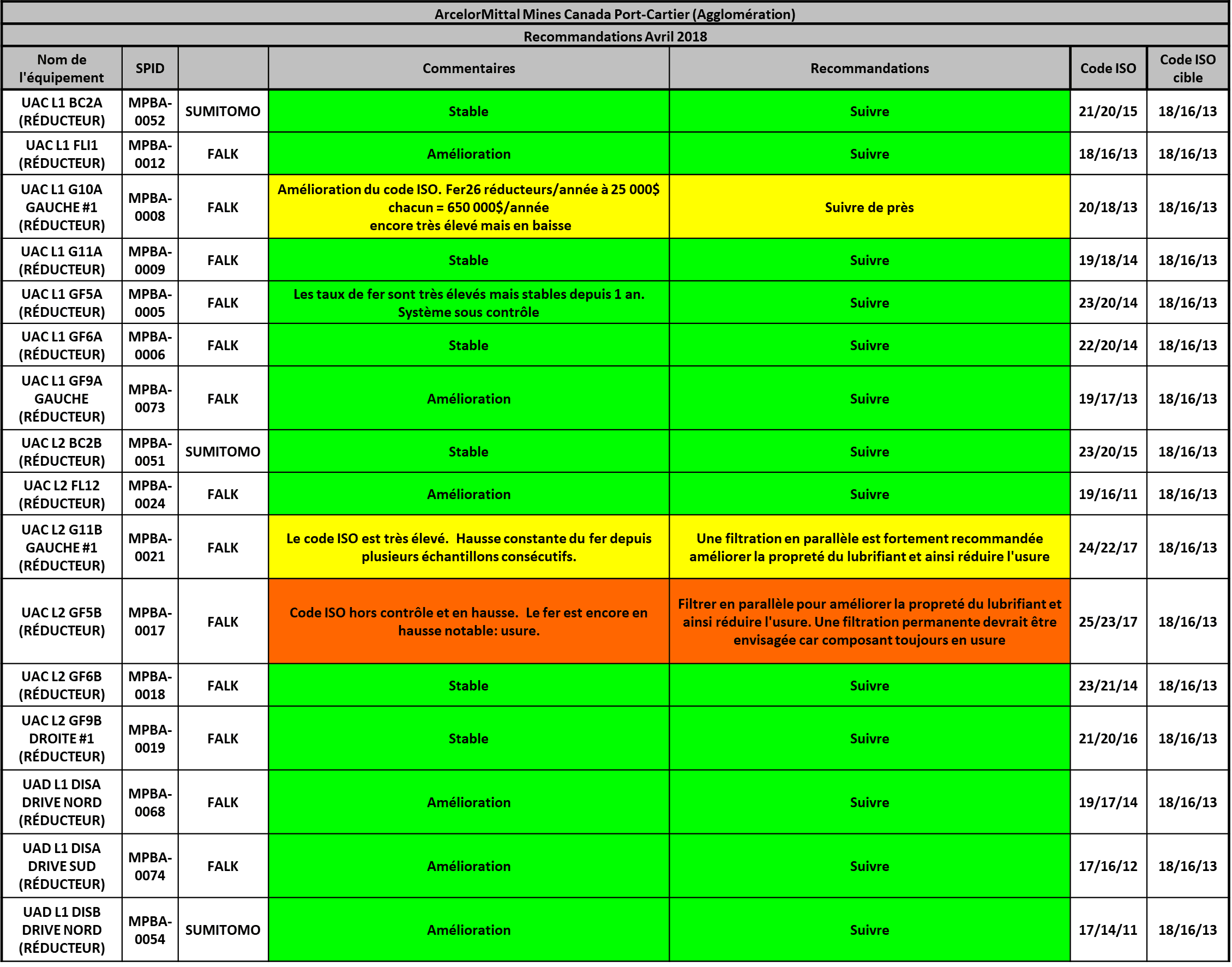
Sample status report mid-program
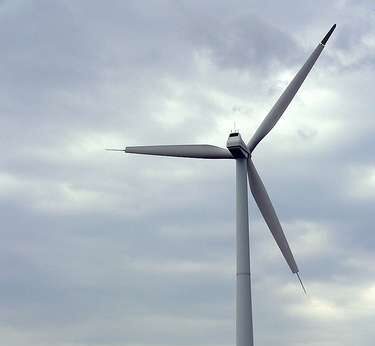
Prochaine étude de cas
Cylindre soudé pour tests de palme d’éolienne
Résoudre les problèmes de fuites récurrentes dans les cylindres utilisés par les clients.