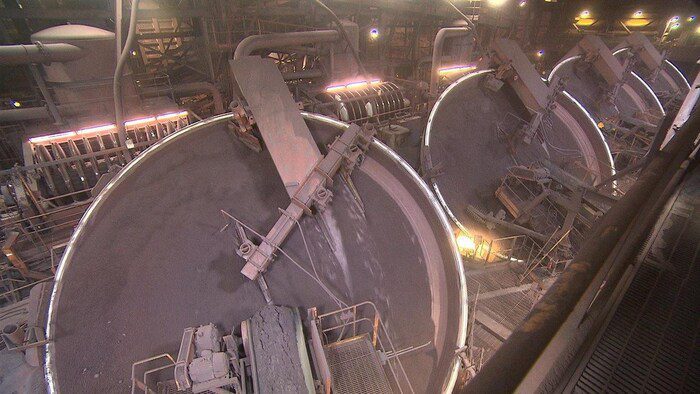
Implementation of an oil analysis global program generating substantial savings
The plant was spending substantial sums on oil waste and gearbox changes with oil being replaced preventively which was costly but also an environmental concern.
Customer’s concerns or issues
Reactive failure measures were costly
The customer was having to change gearboxes on average every two weeks and was proceeding to an oil change at the same time. This process was costly and time consuming and had a negative environmental impact.
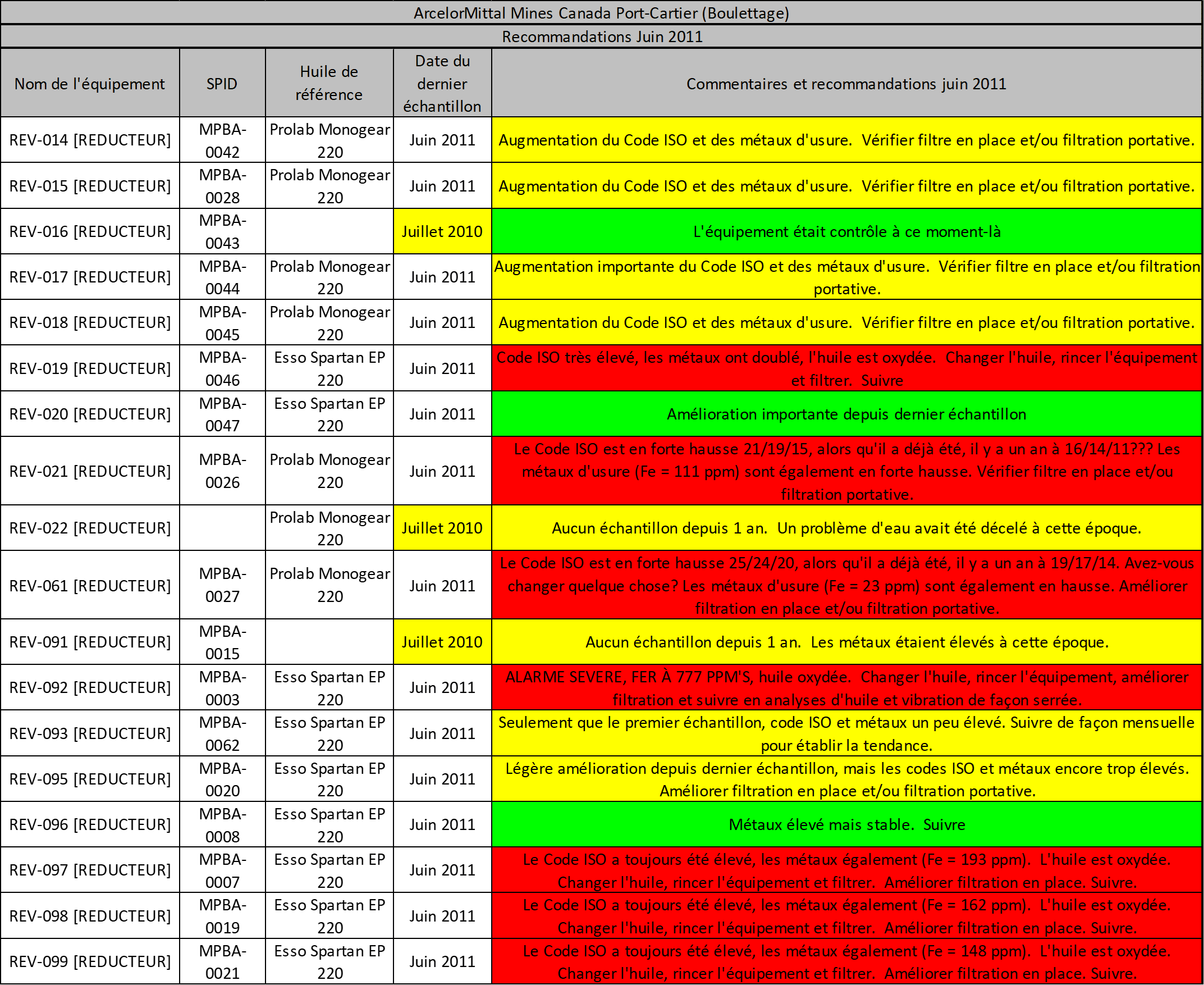
First sampling status report
Benefits of our solution
Proactive maintenance and equipment health tracking
Our solution was to implement a regular health check of the equipment through oil analysis and a comprehensive action plan thus eliminating the need for unscheduled shutdowns. Filtration modifications were made to key components to address the abnormal results and reducing the need to waste the oil before it’s end of life. By moving to a proactive maintenance approach, we were able to save millions in reactive maintenance spendings and shutdowns.
90%
650 000$
4 million of $
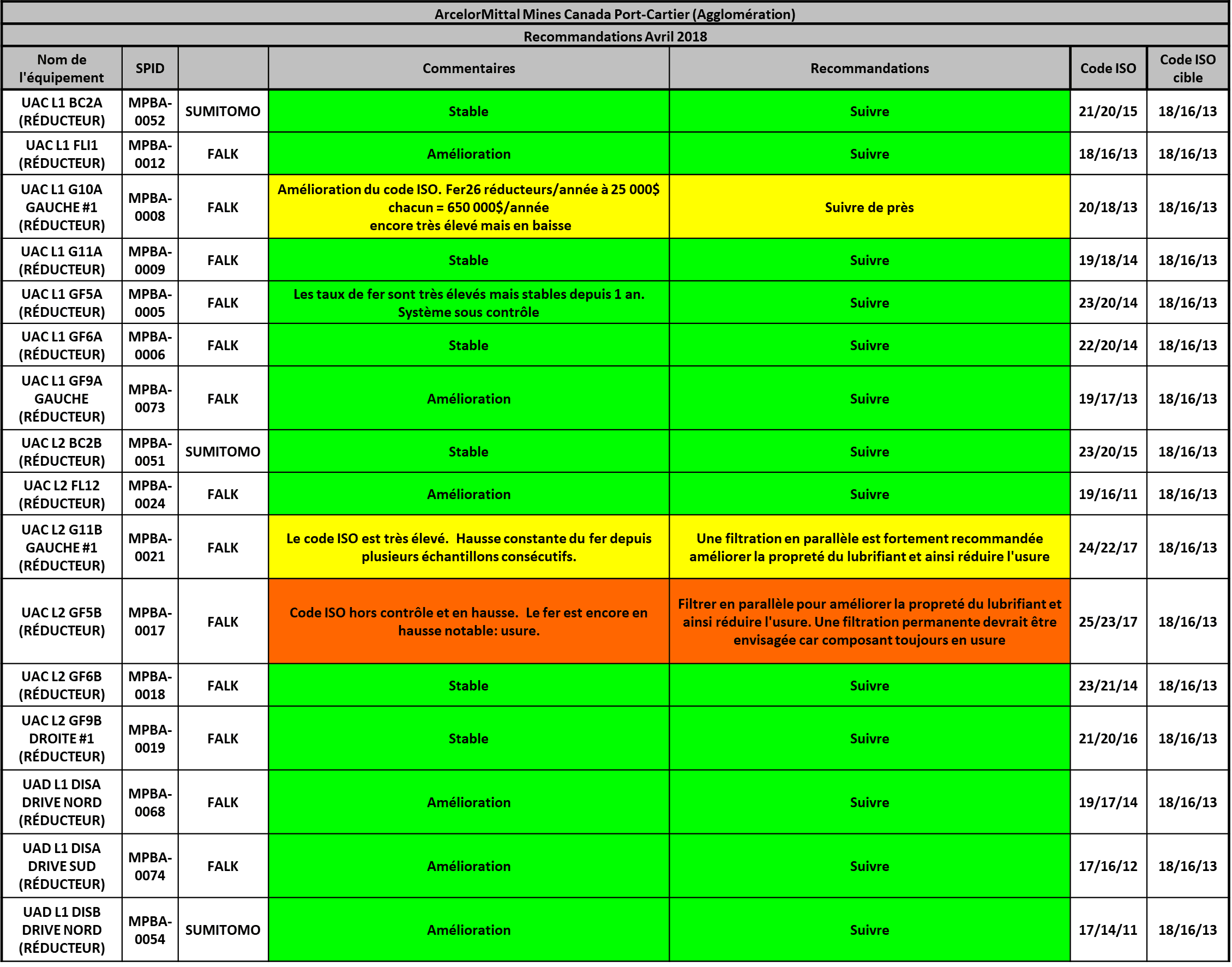
Sample status report mid-program
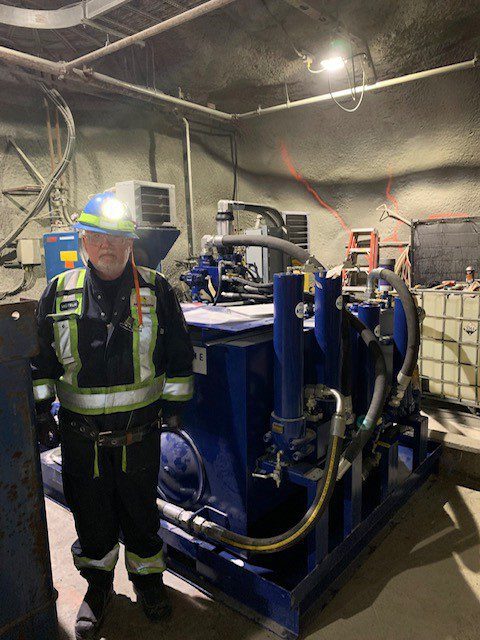
Next case study
Hydraulic system overhaul
Complete overhaul of the Tramac hammer hydraulic system. Non-compliant hydraulic component technology and obsolete filtration.