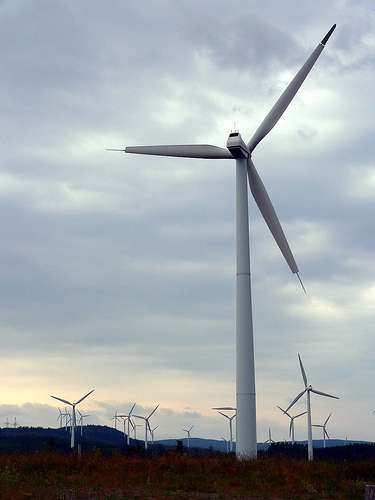
Welded cylinder for windturbine palm testing
The customer had a large number of leaks due their use of NFPA cylinders produced in India and China. While assembling the equipments, they had a number of leaky cylinders that were coming unscrewed due to vibrations. They needed to test the cylinders multiple times to ensure they could deliver a system that had no leaks.
Customer’s concerns or issues
Redesign of their NFPA Cylinder as a welded cylinder
The customer had quality problems with their NFPA cylinders used for clamping the material layers during the blade manufacturing process. Many of the NFPA cylinders they received from their original manufacturer would not hold up to the repeated cycles and vibrations experienced during the production process. Therefore, all cylinders had to be tested multiple times prior to use and would still continue to fail. The cylinders would come loose, releasing the clamping effect on the material, and needed to be changed, delaying the blade assembly process. This consistent failure would add significant time and cost to the blade assembly process.
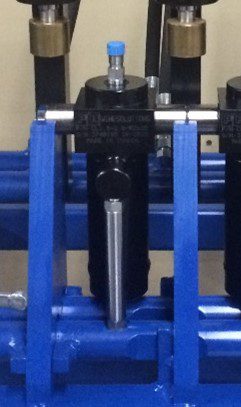
Benefits of our solution
Our solution was to replace the original cylinder with a welded cylinder designed specifically for the application. The new cylinder had fewer parts that could vibrate loose during the blade production process. The persistent leaks were eliminated allowing the cylinder to maintain its clamping force during the entire production cycle. To ensure the assembled cylinder would meet the strict requirements, as part of our manufacturing process, the cylinders were cycled 700 times before being released for shipment to the customer.
80%
0%
120h/week
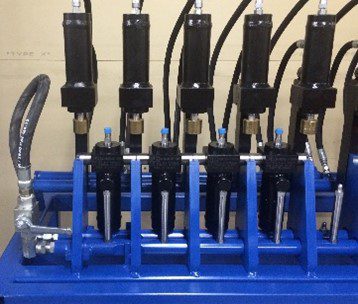
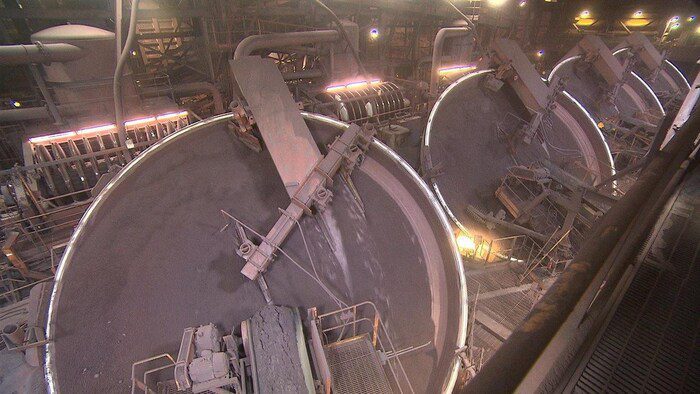
Next case study
Implementation of an oil analysis global program generating substantial savings
The plant was spending substantial sums on oil waste and gearbox changes with oil being replaced preventively which was costly but also an environmental concern.